John Deere Operations Center is an online farm management system that enables access to farm information anytime, anywhere. Operations Center enables smarter machines, enhanced connectivity, and achieving more informed and accurate decision making. Tools in the Operations Center provide you and your partners with the ability to analyze, edit, and make collaborative decisions from the same set of information to get higher yields and reduce input costs. These tools help you farm more efficiently by creating plans and directing in-field work, allowing you to farm more acres in less time.

Combined with its complimentary suite of mobile apps and the power of live connections to the machine, Operations Center enables you to manage your operation more efficiently, do a better job on every pass, reduce costs, and improve profitability.
When it matters most, manage your farm from anywhere.
Nearly 20 years ago, John Deere producers began guiding equipment with global positioning systems (GPS). Connecting machines to this technology empowered them to work with greater precision, efficiency, and ease. This connectivity quickly became the way farms operate. Now, it’s a given. Today, thanks to relentless innovation and advancing technologies, JDLink connectivity opens the way to improve performance in virtually every aspect of your farm operation. The more machines you connect, the more you can achieve – getting more done with less, adding profits, and raising productivity.
JDLink connectivity links you to:
- Your work and results – Make decisions based on your operation's accumulating intelligence. With ready access to past performance, current progress, and future plans, you can take confident steps toward greater efficiency, productivity, and profits.
- Your team – Give your team the information and direction they need to do jobs accurately and on time. When you can reach your crew and they can reach you, you're ready to deal with the unexpected, adjust plans, and solve problems together.
- Your advisors – Easily exchange information with advisors who inform your decisions. With a clear view of what's happened and what's happening in your operation, your trusted partners can offer even more accurate, reliable advice.
- Your equipment – Stay on top of your equipment's health and productivity. With access to monitor and control machines from anywhere, you can prevent or minimize work interruptions, solve problems, and keep business running strong. By passing data from one machine to another, you can take time and guesswork out of mission-critical jobs, ensuring consistently excellent results throughout your production cycle.
- Your dealer – Tap into your dealer's expertise and support to get maximum value from your John Deere investments. With your dealer's vigilant attention, you get proactive service, customized support, and insights and training from the best in the business.
- John Deere – Know that you are running your operation with quality, durability, and innovation using John Deere tools and technologies that are fit for your purpose today and getting smarter all the time, because John Deere learns from and innovates for a global network of connected customers.
As a farm manager, you can’t be everywhere at once. But with JDLink hardware and connectivity, you can easily pay attention to things that worry or cost you most, no matter where you are. JDLink connections allow machine and field data to flow automatically to the John Deere Operations Center application, making it visible and useful to you and your crew. With JDLink, you are always connected to the work in progress and can make timely adjustments to keep things moving, whether you are tilling, planting, applying, or harvesting.
Build your team, connect your equipment, and enter your fields with setup features.
Set up your team:
- Add the correct staff to the organization and assign the appropriate access levels to do their work.
- Establish partnerships with trusted advisors and set access levels so they can effectively support operations.
- Grant appropriate access to connected software companies (CSC) as needed to support operations.
Set up your equipment:
- Build an accurate equipment list of connected machines, implements, and support vehicles.
- Turn on JDLink connectivity to allow automatic machine and agronomic data flow to Operations Center:
- Remotely support operators and make timely adjustments.
- Keep equipment running with dealer remote monitoring and proactive support. - Track locations of the entire fleet in Operations Center with connectivity options for support vehicles.
Set up your farm fields:
- Locate and name fields so your team knows what to do and where to go.
- Set boundaries and guidance lines to keep work on track, improve performance in the field, and improve efficiency throughout the season.
- Flag field obstacles and crop conditions to safely and efficiently identify issues to review later.
Save time and money by planning field work before equipment reach the fields.
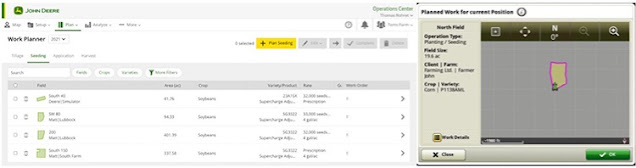
Create your work plan:
- Invest time in your work plan to save money, keep running, and bring back data you can trust.
- Create work plans from anywhere and at any time on any device.
- Determine who does what and where so work gets done efficiently, prioritizing as necessary.
- Create precise prescriptions to get the most out of the field while controlling cost.
- Define the guidance line to make it easy for the operator to work efficiently and minimize compaction.
Send your plan to your equipment:
- Send plans wirelessly (no lost thumb drive, no texts, no calls, and no mistakes).
- Waste no time in the cab; with the push of one button, the operator knows exactly what to do.
- Use only what you need to get the work done right, reduce waste, and protect the environment.
- Ensure what's done in the field is according to the plan.
- Automatically document the work.
Analyze past work to guide decisions for future passes and growing seasons.
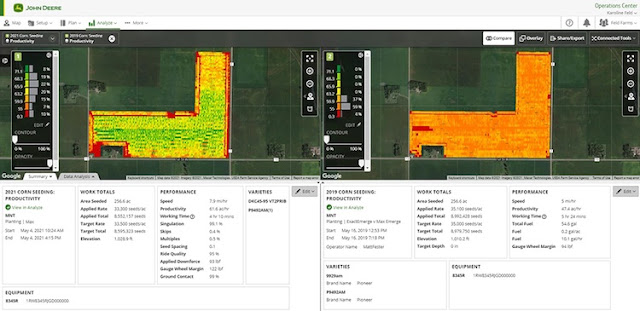
Use data to guide decisions:
- Evaluate equipment purchases using equipment performance data (productivity, throughput, fuel use).
- Review outcomes of product or variety trials to influence future yield.
- Assess work at the zone, field, or farm level.
- Compare machine to fleet performance and utilization to find opportunities for efficiency.
Easily share information:
- Pull bundled field reports to give others a well-rounded picture of the season.
- Quickly filter and sort data to gather information needed in reports.
- Access information for field-level compliance reporting and sustainable practices.
Know more about your people, equipment, and farm with Home and Map features.

Home and Map in John Deere Operations Center helps equipment and operators perform better, ensures the farm runs smoother with less stress, and supports making data-driven decisions confidently.
- Be aware – see where equipment and people are right now on the map. JDLink machines update their location every 5 seconds. The status icon also shows if the equipment is working, idling, or transporting down the road. The progress bar shows acres completed for seeding and harvesting. Simple-to-use filters help find equipment and fields easily.
- Be proactive – know where to send fuel trailers with remote fuel and diesel exhaust fluid (DEF) level monitoring. Diagnostic trouble codes (DTC) instantly show potential equipment issues, and flags help pinpoint items to return to later, such as rocks.
- Be remote – equipment and field totals, performance, and rates are updated every 30 seconds to help understand how work is going and how equipment is performing from anywhere. It’s even possible to remotely see the equipment operator’s display using Remote Display Access to adjust machine settings before it is too late.
By connecting equipment to the Operations Center with JDLink, you can manage your farm from anywhere.
Comments
Post a Comment